Silicone additives are a crucial component in the manufacturing of polymer compounds, playing a pivotal role in enhancing the efficiency and quality of the end product. These additives, derived from silicon, a naturally occurring element, are incorporated into polymers to modify their properties and improve their performance. They serve multiple functions, including reducing viscosity, lowering surface tension, and acting as a lubricant, all of which are essential in the mold filling and release stages of polymer manufacturing.
The process of mold filling and release is a critical aspect of polymer compounds manufacturing. It involves the precise filling of a mold with a polymer melt and its subsequent release once the material has cooled and solidified. This process determines the shape, size, and overall quality of the final product. Any inefficiencies or errors in this stage can lead to defects, waste, and increased production costs. Therefore, the use of silicone additives to improve mold filling and release is of paramount importance in the industry.
Mold Filling
Silicone additives reduce the viscosity of the polymer melt during the mold filling process. This allows the material to flow more easily into the mold, ensuring a more uniform and complete filling. The additives also help to reduce the surface tension of the polymer, which can help to prevent defects such as air bubbles and voids. This results in a higher quality product with fewer imperfections.
Mold Release
Silicone additives also play a key role in the mold release process. They act as a lubricant, reducing the friction between the mold and the polymer. This makes it easier to remove the finished product from the mold without causing damage. Silicone additives can also help to prevent the polymer from sticking to the mold, which can reduce downtime and increase productivity in the manufacturing process.
How silicone additives work in polymer compounds?
Silicone additives work in polymer compounds by modifying their properties and enhancing their performance. They are used to improve the processability, durability, and functionality of the polymers.
Processability: Silicone additives act as processing aids during the manufacturing of polymer compounds. They reduce the viscosity of the polymer melt, making it easier to fill the mold completely and evenly. They also act as a lubricant, reducing friction between the polymer and the mold, which facilitates a smoother release of the finished product from the mold.
Durability: Silicone additives can enhance the durability of polymer compounds. They can improve the heat resistance, weather resistance, and mechanical properties of the polymers, making them more robust and long-lasting.
Functionality: Silicone additives can also enhance the functionality of polymer compounds. They can improve the surface properties of the polymers, making them more resistant to scratches, stains, and water. They can also improve the optical properties of the polymers, making them clearer and more transparent.
How silicone additives improve the efficiency of mold filling?
Silicone additives can enhance the efficiency of mold filling in 5 ways:
- Lowering Viscosity: Silicone additives can lower the viscosity of the polymer melt, allowing it to flow more easily and quickly into the mold. This ensures a more complete and even filling of the mold.
- Reducing Friction: Silicone additives can act as a lubricant, reducing the friction between the polymer melt and the mold. This allows the polymer to fill the mold more smoothly, reducing the likelihood of defects.
- Enhancing Heat Stability: Silicone additives can improve the heat stability of the polymer, preventing premature solidification during the mold filling process. This ensures that the polymer remains in a fluid state for a longer period, allowing for a more efficient mold filling.
- Improving Surface Properties: Silicone additives can enhance the surface properties of the polymer, preventing it from sticking to the mold. This facilitates an easier release of the finished product from the mold, reducing the time and effort required for demolding.
- Reducing Shrinkage: Silicone additives can reduce the shrinkage of the polymer during cooling, ensuring that the finished product retains the exact shape and dimensions of the mold.
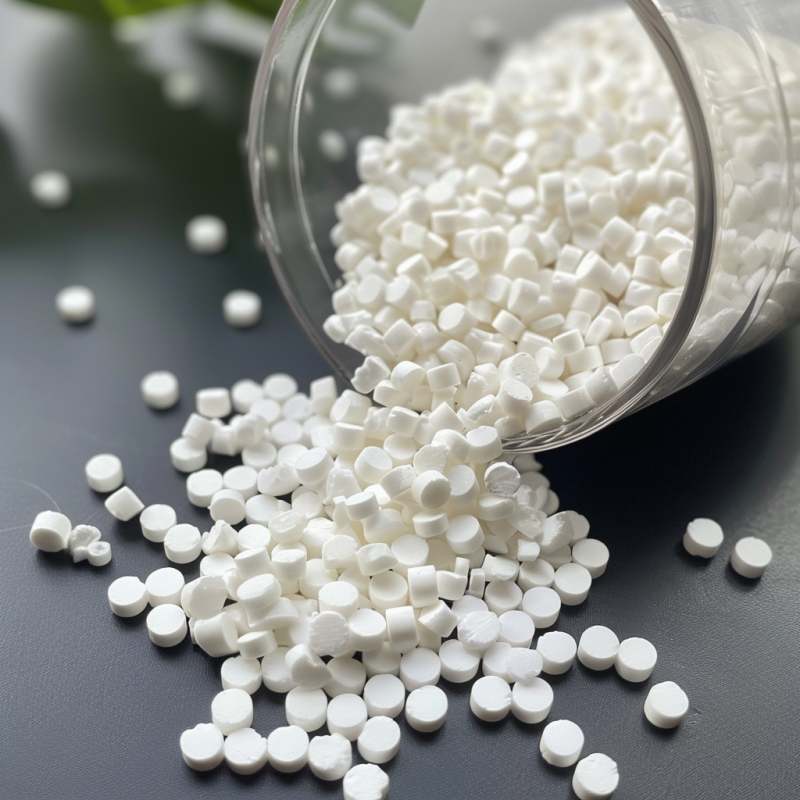
How do silicone additives impact the mold release process?
Silicone additives can make the mold release process more efficient, improve the quality of the finished product, and extend the lifespan of the mold,here 7 ways for your reference:
- Lubrication: Silicone additives can act as a lubricant, reducing the friction between the molded material and the mold. This makes it easier to remove the finished product from the mold without causing damage.
- Non-Stick Properties: Silicone additives can provide non-stick properties to the mold surface. This prevents the molded material from sticking to the mold, facilitating easier and cleaner release.
- Improved Surface Finish: Silicone additives can enhance the surface finish of the molded product. The product comes out of the mold with a smoother and more polished surface, reducing the need for post-molding finishing processes.
- Reduced Material Waste: By ensuring a clean and easy release, silicone additives can help reduce material waste that can occur due to product sticking or tearing in the mold.
- Increased Mold Lifespan: By reducing the stress on the mold during the release process, silicone additives can help to extend the lifespan of the mold.
- Heat Stability: Silicone additives can improve the heat stability of the material, preventing it from sticking to the mold due to overheating. This ensures a smoother and more efficient release process.
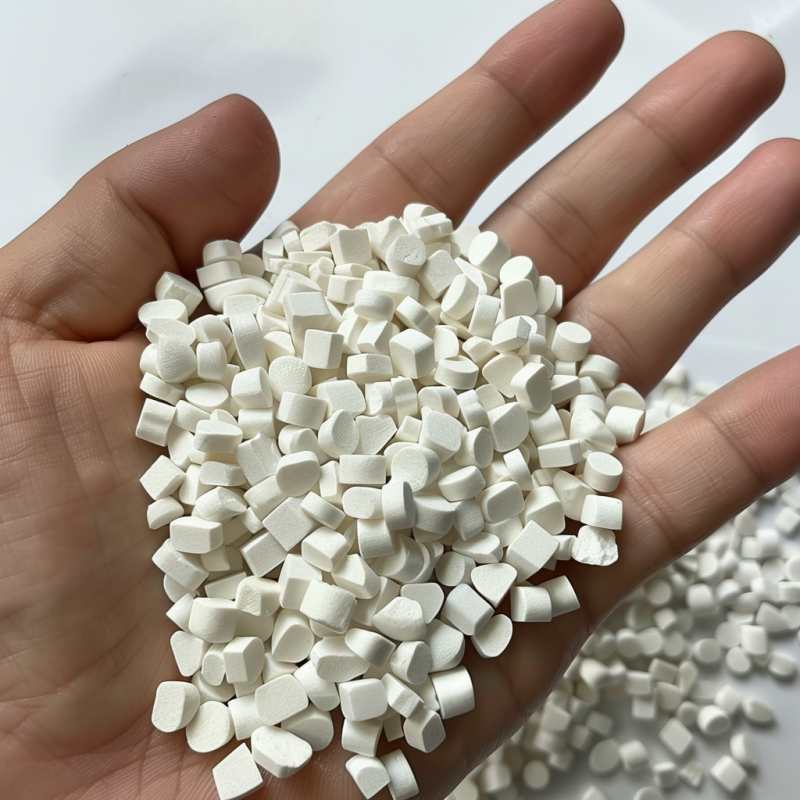
How silicone additives facilitate easier and more efficient mold release?
Silicone additives facilitate easier and more efficient mold release through the following 6 ways:
- Non-Stick Properties: Silicone additives provide a non-stick surface on the mold, preventing the molded material from adhering to the mold. This makes it easier to remove the finished product without causing any damage.
- Lubrication: Silicone additives act as a lubricant, reducing the friction between the mold and the material. This allows for a smoother release of the product from the mold.
- Improved Surface Finish: The use of silicone additives can result in a better surface finish on the molded product. The product comes out of the mold with a smoother and more polished surface, reducing the need for post-molding finishing processes.
- Heat Resistance: Silicone additives can improve the heat resistance of the mold, preventing the material from sticking to the mold due to overheating. This ensures a smoother and more efficient release process.
- Reduced Material Waste: By ensuring a clean and easy release, silicone additives can help reduce material waste that can occur due to product sticking or tearing in the mold.
- Increased Mold Lifespan: By reducing the wear and tear on the mold during the release process, silicone additives can help to extend the lifespan of the mold.
In conclusion, silicone additives are integral to the mold filling and release process in the production of polymer compounds. Their role in enhancing the flow of the polymer, reducing defects, and improving the overall quality of the final product cannot be overstated. The use of these additives not only streamlines the manufacturing process but also significantly reduces waste and production costs.
However, while the benefits of silicone additives are clear, there is still much to explore in this field. The potential for further research and development is vast, with opportunities to discover new applications, improve existing processes, and even develop new types of silicone additives. The continued advancement in this area will undoubtedly contribute to the evolution and growth of the polymer manufacturing industry.