Modified polymer compounds are indispensable in a variety of industries, including automotive, construction, and electronics, due to their unique properties such as durability, flexibility, and resistance to heat and chemicals. These compounds are used in a wide range of applications, from creating car parts to building materials, making their efficient production crucial. However, manufacturing these compounds can be challenging due to their complex nature. This is where silicone processing aids come into the picture. These are special additives used in the production process of modified polymer compounds to enhance their processability and performance. Silicone processing aids help streamline the manufacturing process, reduce production time, and minimize waste, thereby significantly improving manufacturing efficiency. Their role is vital in ensuring the production of high-quality modified polymer compounds in a cost-effective manner.
What are modified polymer compounds?
Modified polymer compounds are essentially polymers that have been chemically altered to improve or change their properties. This can include enhancing their strength, flexibility, heat resistance, or chemical resistance, among other characteristics. The modification process can involve adding certain substances or carrying out specific chemical reactions. The resulting compounds are more versatile and can be tailored to suit a wide range of applications. They are used in various industries, including automotive, construction, and electronics, due to their enhanced properties and performance.
What are types of modified polymer compounds?
There are several types of modified polymer compounds, each with unique properties and uses. Here are seven examples:
- Thermoplastic Elastomers (TPEs): These are a type of polymer that combine the properties of elastomers (rubbers) and thermoplastics. They are flexible and can be stretched, but also melt and can be reshaped when heated.
- High Impact Polystyrene (HIPS): This is a type of polystyrene that has been modified with polybutadiene rubber to make it more impact-resistant.
- Acrylonitrile Butadiene Styrene (ABS): ABS is a common thermoplastic polymer that is often used in injection molding applications. It’s known for its toughness and impact resistance.
- Polyvinyl Chloride (PVC): PVC can be modified to be either rigid or flexible. It’s used in a wide range of products, from pipes and cable insulation to clothing and inflatable products.
- Polyethylene (PE): There are several types of modified polyethylene, including High Density Polyethylene (HDPE), Low Density Polyethylene (LDPE), and Linear Low Density Polyethylene (LLDPE), each with different properties and uses.
- Polypropylene (PP): This is a versatile polymer that can be modified to be used in a variety of applications, from packaging and textiles to automotive parts and medical devices.
- Polycarbonate (PC): PC is a strong, durable polymer that is often used in applications that require transparency, like eyewear and electronic devices.
What are silicone processing aids?
Silicone processing aids are additives used in the processing of various polymers and plastics to improve their performance and ease of manufacturing. They are often used to enhance the flow properties of the material during processing, making it easier to shape and mold.
Here are 5 benefits and uses of silicone processing aids:
- Improved Flow: They can reduce the viscosity of the polymer melt during processing, allowing it to flow more easily into the mold. This can result in better surface finish and detail in the final product.
- Reduced Friction: Silicone processing aids can reduce friction during processing, which can prevent damage to the machinery and reduce energy consumption.
- Enhanced Performance: They can improve the physical properties of the final product, such as its flexibility, durability, and resistance to heat and chemicals.
- Demolding: They can make it easier to remove the finished product from the mold, reducing the risk of damage and improving production efficiency.
- Foam Control: In some applications, silicone processing aids can help to control the formation of foam during processing.
Silicone processing aids are used in a wide range of industries, including automotive, construction, packaging, and electronics. They are particularly useful in the processing of high-performance polymers and engineering plastics.

What are challenges in manufacturing modified polymer compounds?
Manufacturing modified polymer compounds can be a complex process with several challenges, the most 8 challenges as follow:
- Material Compatibility: Different polymers and additives may not mix well, leading to issues like phase separation or poor dispersion, which can affect the final product’s performance.
- Quality Control: Ensuring consistent quality in the final product can be difficult due to the variability in raw materials and processing conditions.
- Processing Difficulties: Some modifications can make the polymer more difficult to process. For instance, they might increase the viscosity, making it harder to mold or extrify.
- Cost Constraints: The use of certain additives or specialized processing techniques can significantly increase the cost of production.
- Environmental Concerns: Some modified polymer compounds can have a significant environmental impact, either due to the use of hazardous materials in their production or because they are not easily recyclable or biodegradable.
- Stability Issues: Some modified polymers may not be stable over time, leading to changes in their properties or performance.
- Regulatory Compliance: Manufacturers must comply with various safety and environmental regulations, which can be challenging especially when working with new or complex polymer modifications.
- Scale-Up: Transferring a process from a laboratory or pilot scale to full-scale production can be challenging, as issues that were not apparent at a smaller scale can become significant at a larger scale.
How do silicone processing aids work in the manufacturing process?
Silicone processing aids are additives used in the manufacturing of various products, particularly in the plastic and rubber industries. They play a crucial role in enhancing the processability and performance of these materials. Here’s how:
Lower Coefficient of Friction
Silicone processing aids reduce the friction between the polymer and the processing machinery. This eases the movement of the material through the equipment, reducing energy consumption and machine wear.
Improved Melt Flow
They enhance the flow characteristics of the polymer during the melting process. This allows for more efficient molding or extrusion, leading to products with better dimensional stability and fewer defects.
Surface Smoothness
Silicone aids can enhance the surface smoothness of the final product, providing a high-quality finish. This is particularly beneficial in applications where the aesthetic appeal of the product is important.
Thermal Stability
They can increase the thermal stability of polymers during processing. This helps prevent material degradation due to high processing temperatures, ensuring the integrity of the final product.
Release Properties
Silicone processing aids can function as release agents, preventing the material from adhering to the mold or processing equipment. This facilitates easier demolding and reduces the likelihood of product defects.
Foam Regulation
In certain applications, silicone aids can help regulate foam formation during processing. This results in products with consistent density and fewer imperfections.
In essence, silicone processing aids are vital for enhancing the efficiency of the manufacturing process, improving the quality of the end product, and extending the lifespan of processing equipment.
What are the benefits of using silicone processing aids in manufacturing?
Silicone processing aids offer several benefits in manufacturing, particularly in the plastics and rubber industries. Here are seven keys benefits:
- Improved Processability: Silicone processing aids enhance the flow properties of the material, making it easier to mold or extrude. This leads to more efficient production and less strain on the machinery.
- Enhanced Surface Finish: They can improve the surface quality of the final product, resulting in a smoother, glossier finish. This is particularly beneficial in applications where aesthetics are important.
- Reduced Friction: By reducing the friction between the material and the processing equipment, silicone aids can reduce wear and tear on machinery, extending its lifespan.
- Better Heat Stability: Silicone processing aids can improve the heat stability of materials during processing, preventing degradation and ensuring the integrity of the final product.
- Easier Release: They can act as release agents, preventing the material from sticking to the mold or processing equipment. This makes demolding easier and reduces the risk of product defects.
- Foam Control: In some applications, silicone aids can help control the formation of foam during processing, leading to products with a more consistent density and fewer defects.
- Cost-Effective: By improving process efficiency and product quality, and reducing machinery wear, silicone processing aids can ultimately lead to cost savings in the manufacturing process.
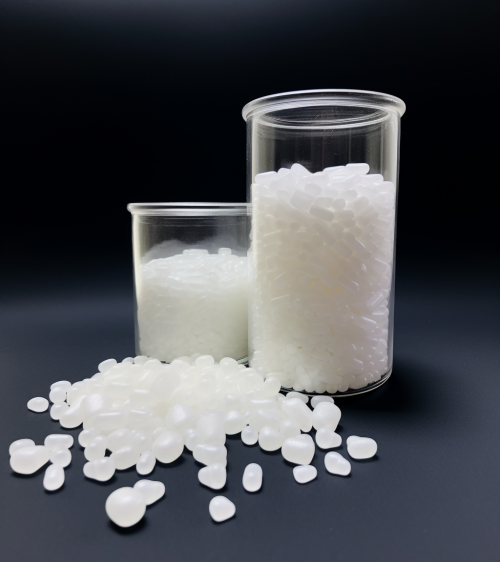
How do silicone processing aids improve manufacturing efficiency?
Silicone processing aids improve manufacturing efficiency in 5 ways:
- Improved Material Flow: They modify the rheology of the material, making it easier to process. This can speed up production times and reduce the energy required for processing.
- Reduced Machine Wear: By reducing friction between the material and the machinery, silicone aids can decrease wear and tear on equipment. This can reduce downtime for maintenance and repairs, increasing overall productivity.
- Faster Demolding: Silicone aids can act as release agents, making it easier to remove products from molds. This can speed up the production cycle and increase the number of units produced in a given time.
- Increased Heat Resistance: They can enhance the heat stability of materials, allowing for higher processing temperatures and faster production rates.
- Reduced Waste: By improving the quality of the final product and reducing the likelihood of defects, silicone aids can decrease waste, leading to more efficient use of materials.
In these ways, silicone processing aids can help to streamline manufacturing processes and boost overall efficiency.
What is the difference in manufacturing efficiency with and without the use of silicone processing aids?
Aspect | Without Silicone Processing Aids | With Silicone Processing Aids |
Material Flow | May not flow smoothly, slowing production and requiring more energy | Improved flow, speeding up production and reducing energy use |
Machine Wear | Increased friction can lead to more wear and tear and frequent maintenance | Reduced friction can decrease wear and tear, extending equipment lifespan |
Demolding | Can be difficult and time-consuming, slowing production | Easier and faster, speeding up production |
Heat Resistance | Materials may not withstand high temperatures well, leading to defects or waste | Enhanced heat stability allows for higher processing temperatures, reducing defects or waste |
Waste | Higher rate of defective products, leading to more waste | Improved product quality can reduce defects and waste |
How can manufacturers switch to using silicone processing aids in their processes?
Switching to silicone processing aids in manufacturing processes involves below 7steps:
- Research: Understand the benefits and potential drawbacks of silicone processing aids. This includes understanding how they can improve efficiency, reduce waste, and enhance product quality.
- Identify Needs: Determine where in the manufacturing process silicone processing aids could be beneficial. This could be in material flow, machine wear, demolding, heat resistance, or waste reduction.
- Supplier Selection: Find a reliable supplier of silicone processing aids. Consider factors such as cost, quality, delivery times, and customer service.
- Testing: Before fully integrating silicone processing aids into the manufacturing process, conduct small-scale tests to ensure they work as expected and do not negatively impact the product or process.
- Training: Train staff on how to properly use silicone processing aids. This includes safety procedures, handling instructions, and how to incorporate them into the existing process.
- Implementation: Gradually incorporate silicone processing aids into the manufacturing process. Monitor the process closely to ensure everything is working as expected.
- Evaluation: Regularly evaluate the effectiveness of the silicone processing aids. Look for improvements in efficiency, reductions in waste, and enhancements in product quality.
What is the future of manufacturing efficiency with the continued use of silicone processing aids?
The future of manufacturing efficiency with the continued use of silicone processing aids looks promising. Here are 6 potential trends and developments for your reference:
1.Enhanced Productivity
As silicone processing aids improve material flow and reduce machine wear, manufacturers can expect to see increased productivity. Faster production times and less downtime for maintenance could significantly boost output.
2.Improved Quality
Silicone processing aids can enhance the quality of finished products by improving heat resistance and making demolding easier. This could lead to fewer defects and less waste, saving resources and improving customer satisfaction.
3.Sustainability
By reducing waste and energy use, silicone processing aids can help make manufacturing processes more sustainable. This is increasingly important as consumers and regulators demand more environmentally friendly practices.
4.Innovation
The continued development and refinement of silicone processing aids could lead to even greater efficiency gains in the future. For example, new formulations could provide better performance or be tailored to specific applications.
5.Cost Savings
All of these factors can contribute to significant cost savings for manufacturers. Lower maintenance costs, reduced waste, and increased productivity can all boost the bottom line.
6.Digitalization and Automation
With the rise of Industry 4.0, the integration of silicone processing aids could be further optimized with digital technologies and automation, leading to even greater efficiencies.
In conclusion, the role of silicone processing aids in enhancing manufacturing efficiency cannot be overstated. These aids have proven to be instrumental in improving material flow, reducing machine wear, and enhancing the overall quality of finished products. They have the potential to significantly increase productivity, reduce waste, and contribute to more sustainable manufacturing practices. As we look towards the future, the continued use and development of silicone processing aids promise to bring even greater efficiency gains. For the industry, this implies a shift towards more cost-effective, sustainable, and high-quality production. It’s a change that not only benefits manufacturers but also consumers and the environment. The implications are far-reaching, signaling a new era of manufacturing where efficiency and sustainability go hand in hand. The future of manufacturing, it seems, will be significantly shaped by the innovative use of silicone processing aids.